增材制造(additive manufacture,AM)又稱“3D打印”,是基于離散-堆積原理,采用與減材制造技術相反的加工方式(逐層累加),最終得到立體實物的過程。具有近凈成形、加工成本低、加工周期短、設計自由度大、節約原材料、節省時間等優點。
目前,增材制造成形材料包含了金屬、非金屬、復合材料、生物材料等,成形工藝能量源包括激光、電子束、特殊波長光源、電弧以及以上能量源的組合,成形尺寸從微納米元器件到10m以上大型航空結構件,在航空航天、國防、工業、醫療、汽車、電子等領域得到了廣泛應用。

增材制造技術的分類及特點
1
無模具快速自由成型,制造周期短,小批量零件生產成本低
增材制造技術因為只需要有加工原料和加工設備就能夠進行產品加工,不需要機械加工和工裝模具,可以實現一次成型,節約了零件的不同工序加工和組裝消耗的時間,進行單件小批量的生產時,增材制造的成本低。
2
零件近凈成型,機加余量小,材料利用率高
增材制造技術因為是一次成型,“自下而上”的“分層制造、逐層疊加”而成型的,材料的損耗大部分是用于對模型成型的支撐上,而絕大部分材料是應用于模型的成型上。因此,增材制造相比傳統減材制造更加的節省原料,也更加的節約能源,因此更經濟些,材料利用率也更高些。
3
激光束能量密度高,可實現傳統難加工材料
激光具有的相干性好、單色性好、方向性好和亮度高的特點,尤其是其高能量束能夠在很短的時間將溫度升高到數千度,在此溫度下絕大部分的金屬都能夠被融化加工成型。因此,傳統的難加工材料如38CrMnSiA、TC4等,都可被加工制造出來。
4
加工的零件結構性強度更高、加工應力集中更小
增材制造技術采用的是一體化制造成型技術,相比由零件間組裝成的整體部件具有更強的剛度和穩定性。另外,增材制造采用的分層制造、逐層疊加的成型技術,在每一片層凝結成型時,已經將成型應力釋放,因此制造的零件沒有應力集中或者應力集中現象很少。
當然,增材制造技術還有很多其他方面的優勢,比如可實現多種材料任意復合制造、加工效率高、不受零件復雜外形限制等。

增材制造技術優勢
01
設計上的自由度
在機加工、鑄造或模塑生產當中,復雜設計的代價高昂,其每項細節都必須通過使用額外的刀具或其它步驟進行制造。相比而言,在增材制造當中,部件的復雜度極少需要或根本無需額外考慮。增材制造可以構建出其它制造工藝所不能實現或無法想像的形狀,可以從純粹考慮功能性的方面來設計部件,而無需考慮與制造相關的限制。
02
小批量生產的經濟性
增材制造過程無需生產或裝配硬模具,且裝夾過程用時較短,因此它不存在那些需要通過大批量生產才能抵消的典型的生產成本。增材工藝允許采用非常低的生產批量,包括單件生產,就能達到經濟合理的打印生產目的。
03
高材料效率
增材制造部件,特別是金屬部件,仍然需要進行機加工。增材制造工序經常不能達到關鍵性部件所要求的最終細節、尺寸和表面光潔度的要求。但是所有近凈成形工藝當中,增材制造是凈成形水平最高的工藝,其后續機加工所必須切削掉的材料數量是很微量的。
04
生產可預測性好
增材制造的構建時間經常可以根據部件設計方案直接預測出來,這意味著生產用時可以預測得很精確。隨著增材制造業的拓展,制造商對于自己的制造時間表編制將擁有嚴密得多的控制力。
05
減少裝配
通過增材制造所構建的復雜形狀可以一體成形,取代那些目前還需采用眾多部件裝配而成的產品。這意味著增材工藝所帶來的節省效果包括了省去了之前需投入到裝配工序的工作量、需涉及的堅固件、釬焊或焊接工序,還有單純為了裝配操作而添加的多余表面形狀和材料。
增材制造的缺點
不可否認,增材制造是一種革命性的制造技術,但仍然存在一些挑戰:
難以將生產規模擴大到大規模制造水平
大多數 3D 打印機的打印尺寸有限
某些技術或材料需要大量的后處理
值得注意的是,增材制造技術正在不斷飛躍,制造商和打印機開發商正為現有的生產問題提出新的解決方案。
增材制造的應用領域
航空航天領域
在航天領域,尤其是航天器零部件和天線等結構方面的領域,得益于太空的零(微)重力環境,在軌增材制造可以打印很多傳統加工方式難以實現的零部件。
在航空領域,增材制造的應用逐漸成熟,從最初在非關鍵部件上的應用逐漸過渡到例如發動機核心部件的制造。例如使用增材制造燃油噴嘴,在減少部件的同時,提高燃油效率。
在可以預見的將來,增材制造將在航空領域大放異彩,乃至于影響到飛機的整體設計。另外,3D打印為新型可變機翼的研發提供了強大的加工能力,顯著提高了新型結構的研發效率,并實現了應用于可變機翼的全新的結構體系。

生物醫療領域
隨著人口老齡化進程的急速加快和人均可支出醫療費用的增加,健康問題也逐漸成為人們所密切關注的問題,由此也促進了國內外醫療植入物市場的大爆發。
3D打印技術由于可根據患者需求個性化地定制植入體形狀,并且精確控制植入物的復雜微觀結構,從而實現植入物外形和力學性能與人體自身骨的雙重適配,主要應用于齒科、骨科及顱頜面外科等硬組織的修復和替代醫療硬植體市場。經歷了近20年的發展歷程,金屬3D打印醫療植入物技術逐漸成熟,實現從基礎研究向應用轉化發展。
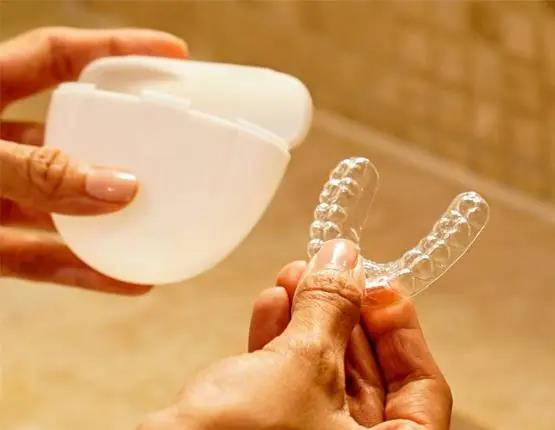

汽車生產領域
隨著汽車產品更新換代的速度越來越快,環保法規日益嚴格,對汽車輕量化要求日益提高,千篇一律的汽車外形不再能滿足客戶的消費要求,個性化定制的需求越來越強烈等急迫需求,3D打印因其無需開模,可節省產品開發的成本和時間,不受模具限制,可隨意打印復雜型面及異形結構,在推動產品快速化、輕量化、定制化方面的優勢給汽車帶來了新的機遇,目前已被大量運用于汽車生產制造的各個環節。
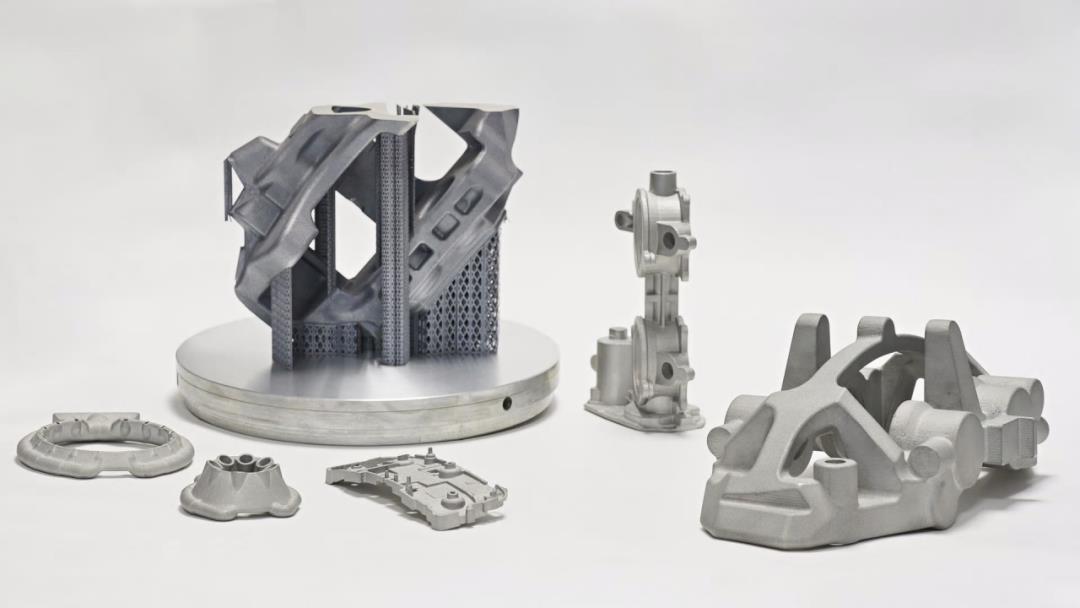
電子設備領域
在現代微波通訊系統及電磁應用領域中,增材制造技術為器件的小型化、輕質化、高精度、低成本制造提供了新方法,可有效降低傳統制造中存在的材料冗余、裝配誤差等缺點。在未來微波及太赫茲器件的增材制造技術發展方面,提升制造質量和速度,研發新材料以適應多功能需求以及實現更高頻器件制造將具有廣闊空間。隨著5G時代的到來和無線充電技術的發展,陶瓷材料的AM有望在新型手機背板的開發上發揮重要作用。
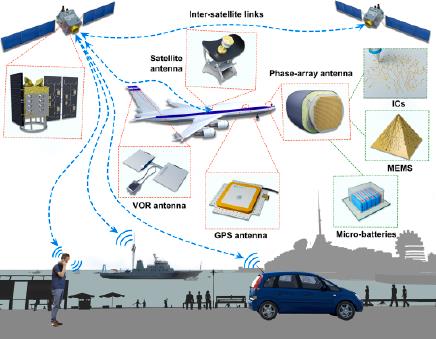
建筑領域
3D 打印建筑方法有望以更少的人更快、更便宜、更準確地建造房屋。3D 建筑公司還表示,他們的材料將比大多數傳統建筑材料更耐用,更堅固。有了這些好處,難怪 3D 打印建筑正在獲得動力。事實上,全球建筑機器人市場(不久前還不存在的東西)預計將在未來五年內增長近 20%。
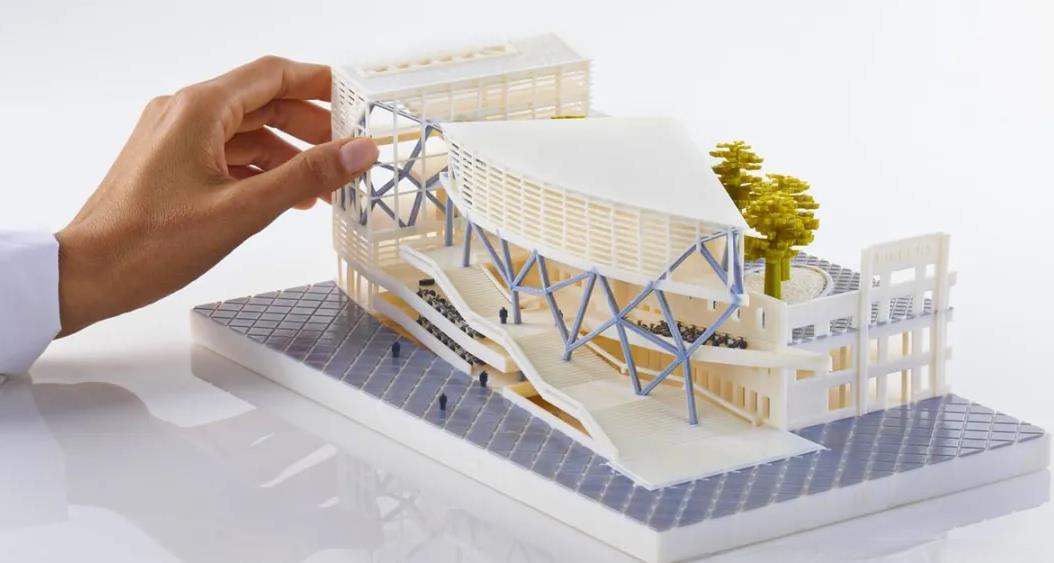
消費品領域
當然,增材制造也為所有消費品生產商提供了多種好處,尤其是在快速原型制作方面。設計師可以在幾個小時內提出一個新的產品概念并打印出一個功能原型,并在幾周內準備好上市的新產品。
快速原型設計使企業家和大型企業都能夠加快產品開發周期。產品的多個版本可以同時在內部進行 3D 打印,并且對材料沒有限制。
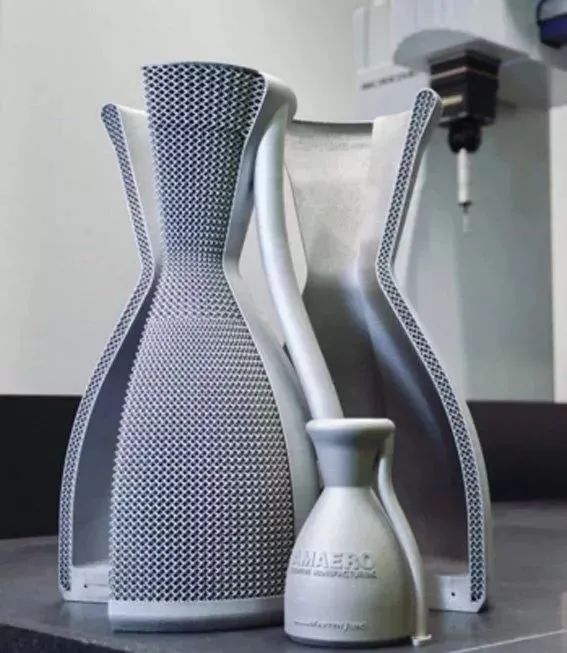
增材制造軟件

每個增材制造的產品都是從數字 3D 模型開始的,幾乎所有產品都是使用 CAD(計算機輔助設計)軟件創建的。
在為增材制造創建 3D 模型時,設計人員通常會應用增材制造設計 (DfAM) 的原則。3D 建模師使用 DfAM 原理在 CAD 軟件中繪制產品模型。他們必須考慮材料的特性和將用于零件的 3D 打印技術,例如材料收縮,同時還要應用拓撲優化、支座規劃和晶格結構等技術來優化增材制造零件。
增材制造商使用的其他軟件包括:
3D 掃描應用
打印準備軟件
仿真軟件
3D 打印機操作系統
若您對3D打印的廣闊世界充滿好奇,渴望深入了解其技術細節與最新動態,請隨時與我們取得聯系。我們期待與您一同探索這一革命性技術的無限潛力。
免責聲明
- 凡本網注明“來源:化工儀器網”的所有作品,均為浙江興旺寶明通網絡有限公司-化工儀器網合法擁有版權或有權使用的作品,未經本網授權不得轉載、摘編或利用其它方式使用上述作品。已經本網授權使用作品的,應在授權范圍內使用,并注明“來源:化工儀器網”。違反上述聲明者,本網將追究其相關法律責任。
- 本網轉載并注明自其他來源(非化工儀器網)的作品,目的在于傳遞更多信息,并不代表本網贊同其觀點和對其真實性負責,不承擔此類作品侵權行為的直接責任及連帶責任。其他媒體、網站或個人從本網轉載時,必須保留本網注明的作品第一來源,并自負版權等法律責任。
- 如涉及作品內容、版權等問題,請在作品發表之日起一周內與本網聯系,否則視為放棄相關權利。